Copper is an essential component in our modern manufacturing world, appearing in various elements, from electrical wires to intricate parts in smartphones and renewable energy systems. This vital metal has formed human civilization for millennia and continues to develop its roles. The copper mining process begins with the ore coming from deep underground to become refined metal. This article will break down this process into 8 clear steps so that you can see how fascinating the journey is. Let’s check it out!
Top Locations for Copper Deposits Worldwide
The global copper supply chain centers predominantly around Chile, which leads world production at 27% as of 2021, according to the World Economic Forum. Peru follows as the second-largest producer at 10% globally. Meanwhile, the Democratic Republic of Congo and China each contribute 8% to global output. Other major copper producers include the United States, Australia, Indonesia, Russia, Canada, and Mexico.
Copper deposits are naturally sedimentary rocks that go through geological processes of hot waters and volcanic activity. These formations are rich in minerals, containing copper ores that can create pure copper through extraction and processing.
Pure copper has superior electrical and thermal conductivity compared to other commercial metals. That’s why electrical and electronic applications consume over half of global copper production.
8 Key Steps of the Copper Mining Process
Raw copper ore undergoes a transformation process before reaching consumers as finished products. The journey of copper begins underground and progresses through eight distinct stages:
- Mining
- Grinding
- Concentrating
- Roasting
- Smelting
- Conversion
- Anode Casting
- Electro-Refining
Mining
Mining is the initial phase of copper processing, beginning with extracting ore from deep underground. There are two main extraction methods: open-pit mining and underground mining. At this stage, sulfide and oxide ores undergo similar extraction and transportation procedures.
Crushing and Grinding
The extracted copper ore, initially in large boulder form, undergoes a crucial size reduction process. Large industrial crushers break down these massive rocks into manageable fragments. Subsequently, grinding mills pulverize these pieces further into fine particles, creating material suitable for efficient transportation and processing at production facilities.
Concentrating
Copper is concentrated with distinct processing paths based on its mineral composition. Oxide ores undergo hydrometallurgical processing (leaching) after crushing, while sulfide ores require additional separation through a process called froth flotation. Then, the bubbling process separates valuable copper minerals from waste rock to collect copper.

Professional laboratory analysis from Ledoux & Company can confirm the quality of copper concentrates before further processing. Our advanced ISO 17025 accredited analysis determines precise copper content plus associated precious metals like gold and silver within the concentrate.
Roasting
Roasting heats sulfide ores to convert sulfides into oxides, facilitating further smelting and purification.
Leaching
Crushed ore is placed on an impermeable surface slopes slightly. Here, sulfuric acid solution sprays across it and flows downward through the heap to dissolve copper content from oxide ores.
Smelting
Copper concentrate undergoes a high temperature at 1260°C in specialized furnaces. This intense heat treatment transforms it into a molten form for further refinement.
Conversion
The heated liquid is poured into a slag-settling furnace to create copper matte with around 60% copper plus slag material. After that, the matte moves to a converter that removes iron and sulfur to yield 98% pure blister copper.
Anode Casting
Oxygen burns off the copper as it changes color from yellow to blue-green. At the end of this stage, molten anode copper flows into molds on anode-casting wheels.
Electro-Refining
The final electro-refining phase in the copper mining process places copper anode slabs in tanks filled with copper sulfate and sulfuric acid solution. Then, pure copper cathode sheets lead to the production of refined copper cathodes.
Recycling Copper
Copper recycling serves as a valuable alternative to traditional mining, as it involves melting and purifying used copper materials to create fresh components. The process supplies about 50% of manufacturing needs, as demonstrated in 2010 when 770,000 metric tons of recycled copper generated six billion dollars in value, making recycling and mining the two primary methods for copper production.
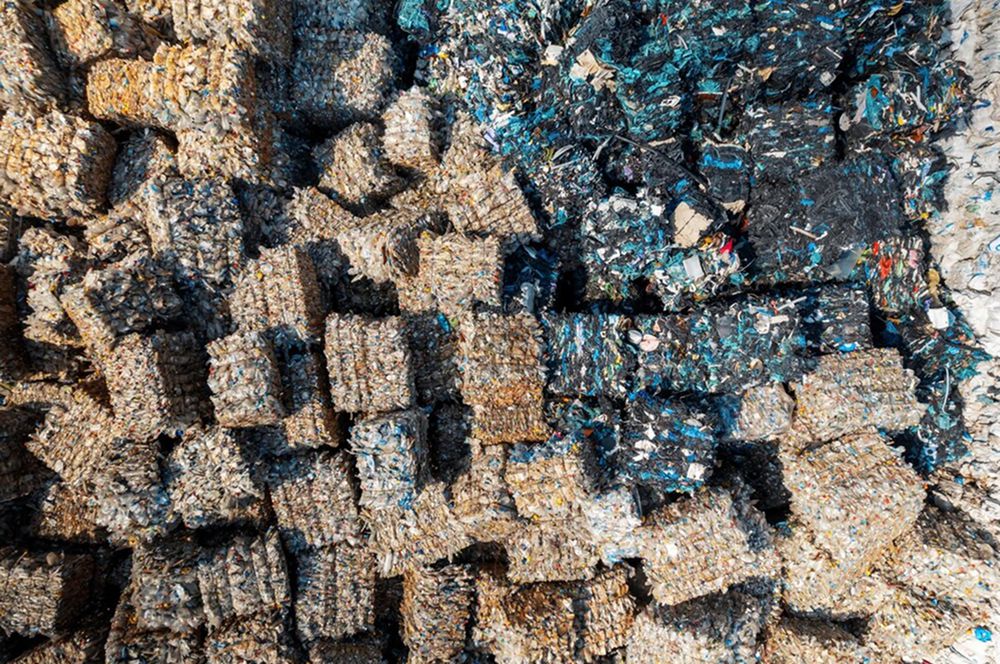
Techniques for Different Ores
Different copper ores require specific processing methods based on their chemical composition, as each type contains unique mineral structures that demand distinct extraction approaches.
Processing of Oxide Ore
The oxide ore processing applies hydrometallurgy, which extracts copper through water-based solutions at room temperature. This method includes three main steps: heap leaching extracts the copper through acid solutions, solvent extraction removes impurities through chemical separation, and electrowinning applies an electrical current for final purification into pure copper sheets.
Processing of Sulfide Ore
Sulfide ore processing relies on pyrometallurgy, which involves extraction methods at high temperatures. The process consists of four key stages: separate valuable minerals through bubbles, concentrate the copper particles into a denser form, melt the ore at extreme temperatures to remove impurities, and run an electrical current through the copper solution to produce highly pure copper cathodes.
Copper Mining Methods
The copper mining process begins with loosening rock formations within the ore body for subsequent extraction plus processing.
The most common method, open pit mining, extracts copper ore located close to the surface. This technique creates benches or terraces, allowing miners to progressively access deeper ore deposits.
When copper deposits lie deep underground, we need underground mining methods. This process involves digging vertical shafts or horizontal tunnels to reach the ore veins. As miners follow these veins, the underground network expands.
Both mining approaches require the transportation of the extracted ore to processing facilities. Large trucks and freight trains move the ore through established routes to refineries, where it undergoes further treatment.
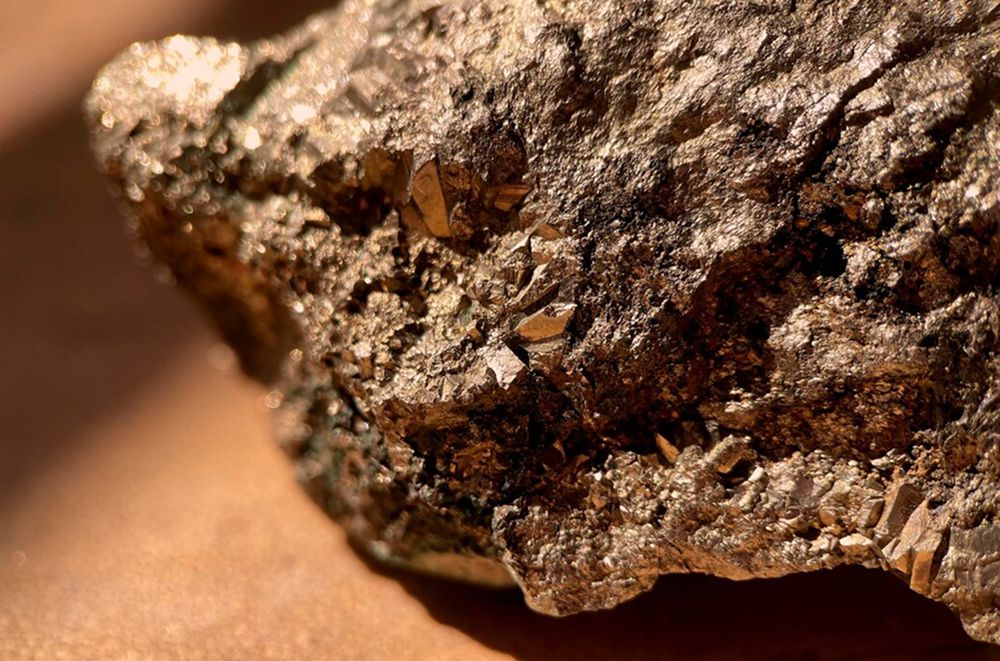
Analyzing accurate copper content is a fundamental step before a refining process. Ledoux & Company is an accredited laboratory that provides precise assay results through professional copper testing services.
Our laboratory analyzes various forms of copper materials, including raw ore, mining products, plus concentrated deposits. Each sample undergoes a thorough examination to determine its exact mineral composition.
Additionally, Ledoux & Company Mexico specializes in evaluating recycled copper materials. Our expert analysis helps businesses recover valuable metals efficiently while meeting industry standards. This comprehensive testing supports both mining operations plus recycling initiatives in the copper industry.
Optimize Your Copper Extraction Process with Ledoux
The copper mining process combines advanced extraction methods plus precise analytical procedures to produce high-quality copper. Each step requires careful attention to detail, while professional testing services play a key role in achieving optimal results.
Ledoux & Company brings expert analysis to your copper mining operations. Our accredited laboratory provides accurate assay results for all types of copper materials. We support both traditional mining plus recycling initiatives through reliable testing services.
Connect with our team today, and let us help you achieve better results through professional copper analysis services!